Vetotop EC393
High performance, two-component, chemically resistant Novolac epoxy coating.
Vetotop EC393 is a high performance, two-component, solvent-free, 100% solids, chemically resistant Novolac epoxy coating engineered for chemical and mechanical resistance in industrial environments. Designed for use on concrete and other hard substrates, Vetotop EC393 delivers exceptional durability against aggressive chemical exposure, including concentrated acids, alkalis, solvents, and a wide range of industrial chemicals.
Vetotop EC393 may be applied as a standalone high-build coating or used in combination with anti-slip aggregates to achieve tailored slip resistance profiles. It is ideally suited for areas requiring high wear resistance and longterm protection, such as chemical processing plants, refineries, battery rooms, and food and beverage production facilities. It may also be reinforced with glass flake additives or fiberglass mesh to enhance structural performance and chemical resistance, particularly in immersion or splash-and-spill zones.
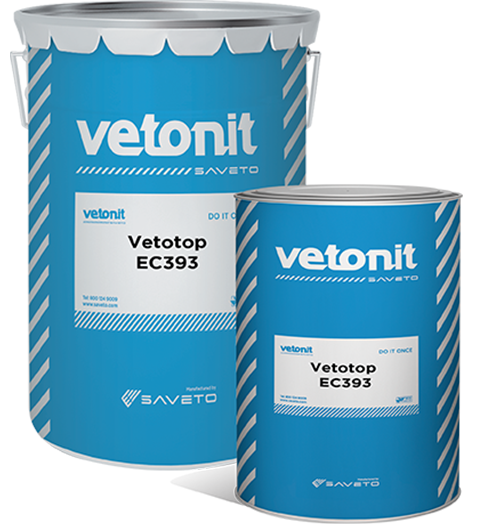
Uses
- Suitable for application on concrete, steel, and masonry substrates, providing long-lasting protection against chemical exposure and physical abrasion in the most challenging service conditions.
- Used in food and beverage production areas, pharmaceutical and clean room environments, laboratories and electronic assembly zones, acid-etching and electroplating operations, industrial kitchens and wet processing areas.
- Ideal for chemical processing and storage facilities.
- Battery manufacturing and charging stations.
- Petrochemical plants and refineries.
- Car parks, garages, and aircraft hangars.
- Waste treatment and containment zones.
Advantages
- Exceptional chemical resistance..
- Excellent abrasion and impact resistance.
- Hygienic, seamless, and easy-to-clean finish.
- Adheres to multiple substrates including concrete, steel, and masonry.
- Fast curing properties for reduced downtime and accelerated return to service.
- Versatile application methods – can be used as a coating, topping, or binder in slurry/broadcast systems.
- Customizable slip resistance, with the option of incorporating aggregates for varied textures.
- Low odor.
- Low VOC content.
Usage Instructions
Surfaces must be clean, dry, and free from laitance, dust, oil, grease, curing compounds, loose materials, existing coatings, and other bond-inhibiting substances.
Concrete must have a minimum compressive strength of 25 N/mm2 and a minimum pull-off strength of 1.5 N/mm2. Mechanical surface profiling is required to achieve an opentextured, laitance-free finish. Recommended methods include vacuum-assisted shot blasting, grit blasting, or wet sanding/grinding. All residual dust must be removed using an industrial vacuum. Avoid over-blasting, which may reduce coverage rates or cause “tracking” through the topcoat. Steel surfaces must be free of excessive rust scale, pollution fallout, dirt, grease, surface chemicals, or any other foreign contaminants prior to abrasive blast cleaning. Apply Vetotop EC393 immediately after preparation to prevent flash rusting.
Priming is mandatory on concrete substrates. For moisture-tolerant performance or when substrate moisture exceeds 4%, apply a suitable epoxy-based primer or moisture barrier from the Vetoprime EP range.
The primer must be allowed to cure until tack-free, and any pinholes or voids must be addressed to ensure uniform coverage.
Vetotop EC393 is supplied in pre-measured kits comprising of Part A (resin) and Part B (hardener) and must be mixed in the prescribed ratio to achieve optimum performance. Prior to mixing together, each component (Part A and Part B) should be mechanically mixed separately for at least 30 seconds to ensure uniform consistency and eliminate any settled material.
Transfer the entire contents of Part B (hardener) into the container of Part A (resin). Mix the combined materials using a low-speed mechanical stirrer (300–450 rpm) equipped with a spiral epoxy paddle (e.g., Jiffy or Exomixer type). Mix thoroughly for 2–3 minutes until a uniform, streak-free blend is achieved. Keep the paddle fully submerged during mixing to avoid air entrapment. Scrape the sides and bottom of the mixing vessel at least once during the process using a flat edge trowel or spatula to ensure complete incorporation of all material. Do not hand mix. Always use mechanical means for consistent results.
Note: Mix only the quantity that can be applied within the working time of the product under prevailing site conditions. Elevated temperatures will shorten pot life; cooler conditions may extend it.
Pour Vetotop EC393 onto the primed surface in a ribbon formation (approximately 150–300 mm wide). Spread evenly using a notched or flat squeegee, steel trowel, or spiked rake to the desired thickness. While the material is still wet, back-roll with a short-nap, solvent-resistant roller (10 mm) to achieve a uniform finish and eliminate squeegee lines. Avoid over-rolling or delayed back rolling, as this may cause bubbling, whitening, or roller marks.
For anti-slip finishes, broadcast pre-dried, non-reactive aggregate into the wet coating to rejection. Allow to cure, then sweep, grind, and vacuum excess material before applying the topcoat. If a topcoat is required for aesthetics, slip resistance, or UV resistance, apply a second layer of Vetotop EC393 using the same method. Adjust application rate and aggregate content based on desired texture and performance.
Allow appropriate curing time before recoating or opening to traffic, based on temperature and ventilation conditions.
Vetotop EC393 begins to cure rapidly under standard ambient conditions, reaching a tack-free state within approximately 4 to 6 hours at 23°C and 50% relative humidity. Light foot traffic may be permitted after 24 hours; however, the system must be allowed to cure fully for a minimum of 7 days to achieve its designed level of chemical resistance and long-term performance.
The recommended recoat window is 12 to 24 hours, depending on site conditions. Low temperatures or high humidity can significantly extend curing and delay reapplication.
All tools and application equipment should be cleaned immediately after use with Vetonit Solvent XX400. Hardened or cured material can only be removed by mechanical means.